Come to check our Corrosion Protection plan
Problems of vehicles on the deck of bulk carriers in maritime transportation at present
a. Chassis part – Transmission & Power Take-off (PTO)
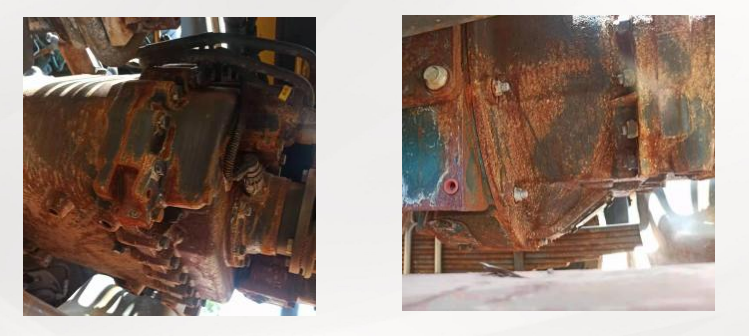
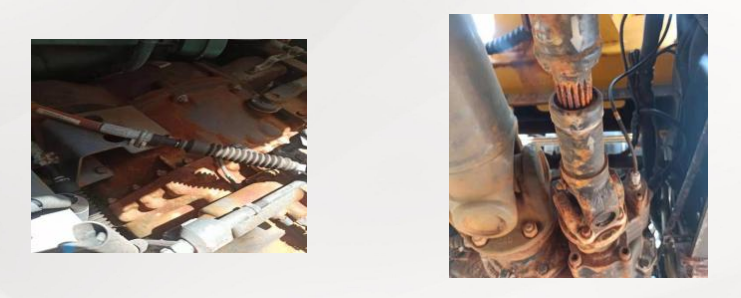
b. Chassis part – Axle & Suspension
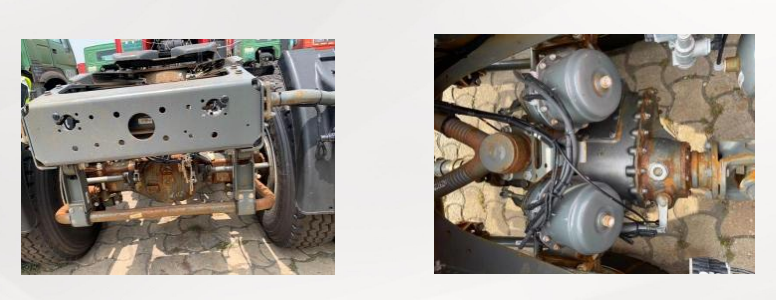
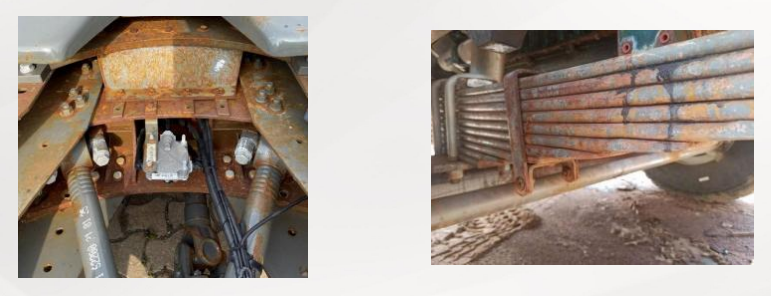
c. Engine accessories
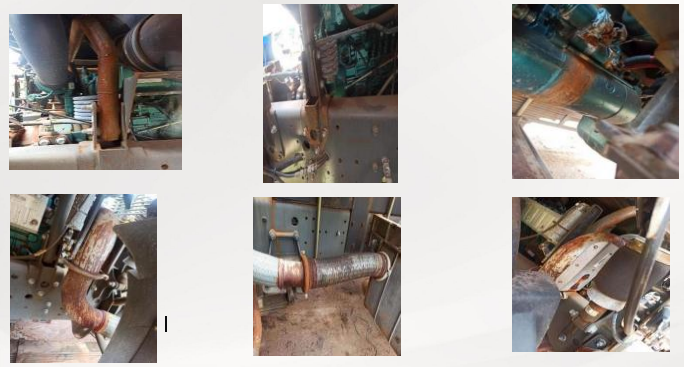
d. Other chassis accessories
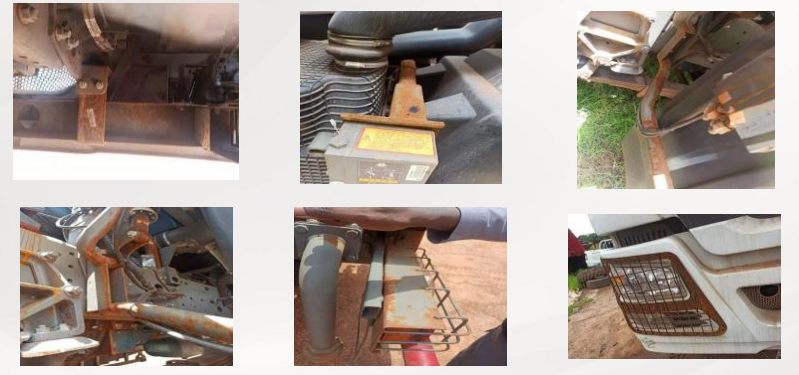
f. Superstructure part – Water tanker
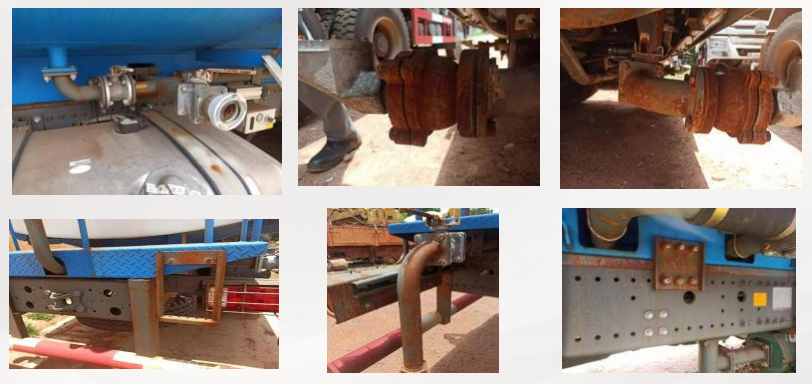
f. Superstructure part – Dump truck
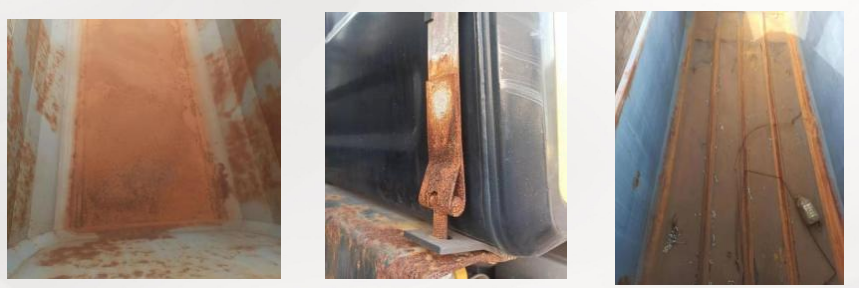
f. Superstructure part – Truck-mounted crane
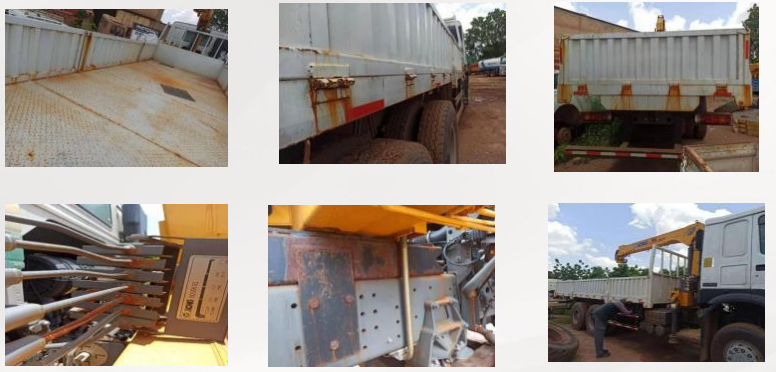
g. The quality of the vehicle cover is poor and it is prone to damage.
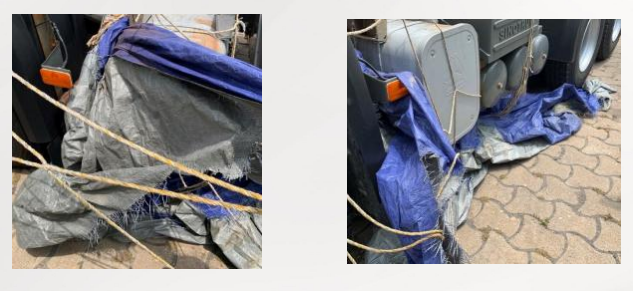
Introduction to the Wax Spraying Anti-corrosion Scheme for Shipment by Sea Bulk Carrier
I. Scheme Objectives
To address the serious rusting problem of export vehicles caused by the sea transportation method of bulk carriers, the entire vehicle surface shall be protected in accordance with this scheme before loading onto the ship, in order to deal with the corrosion and damage of the vehicle paint surface by seawater, ultraviolet rays and sea salt spray.
II. Main Directions of Scheme Implementation
- The main method for the entire vehicle is to spray imported protective wax. It is required to spray the entire vehicle without dead angles, and strictly implement the viscosity of the protective wax and the thickness of the wax film in accordance with the requirements of the scheme.
- For moving parts and bolt positions of important parts, apply ordinary grease.
- For the starting motors, generators and other parts on the engine that rusted in the early stage, apply anti-rust oil and separately wrap them with a vapor-phase anti-rust film.
- For the engine exhaust pipe, conduct a separate local colorless polyurea paint treatment.
- Finally, cooperate with a vehicle cover when loading onto the ship.
III. Main Technical Standards of the Scheme
- Protective wax brand: Ecolab
- Model: YDK – XF01 (customized version)
- Specification: 15 – 20KG
- Specification of the spray gun head for wax spraying: 1.5 – 3.0 caliber.
- Equipped with an extended rod: 50cm – 100cm
- Viscosity of the protective wax: 18 – 28s.
- Requirements for the thickness of the protective wax film: 100 – 150um (wet film) (the thickness of an ordinary wax – sprayed film is 30 – 50um). In order to ensure the thickness of the wax film, after spraying once, it is necessary to wait until it dries and then spray again for supplementary spraying.
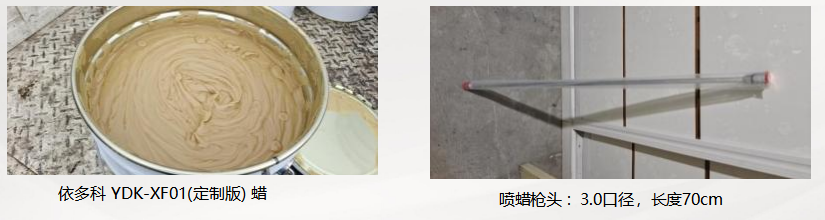
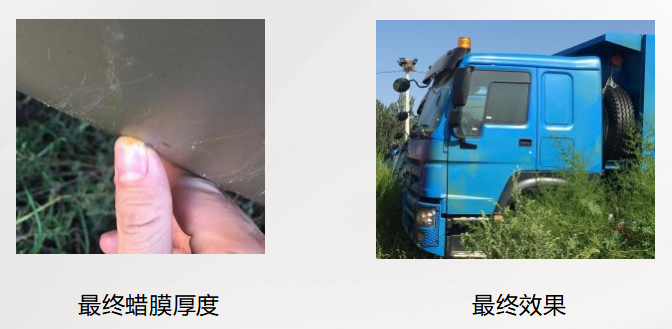
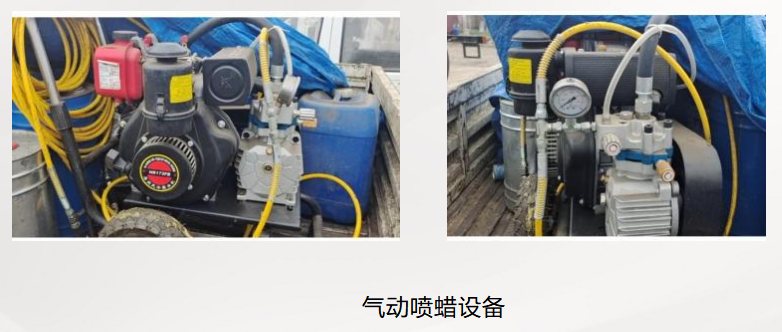
IV. Scheme Implementation (Taking a Dump Truck as an Example)
- After the vehicle has completed the entrusted modification and been stored in the warehouse, park it in an open area that meets the operating conditions for vehicle cleaning, cargo box lifting, and wax spraying. (It is advisable for the Resources Department to coordinate with the superstructure factory to provide an operating area for convenient construction.)
- Vehicle Cleaning
(1) Lift the cargo box of the vehicle to a safe working position, open the support rod, and prop it against the bottom of the cargo box.
(2) Wash the vehicle with water. For stains that cannot be washed off with water, you can use a gauze dipped in a cleaning agent for cleaning. It is required that the surface is free of oil stains, soil, and dust.
(3) Use compressed air to blow out the accumulated water in the water accumulation areas, and then dry the water stains.
(4) Check whether there are any dents or scratches on the surface coating of the entire vehicle. For the dented or scratched areas, they need to be repaired according to the existing paint repair process.
(5) After it is completely dry, that is, when there are no visible water stains, the next process can be carried out.
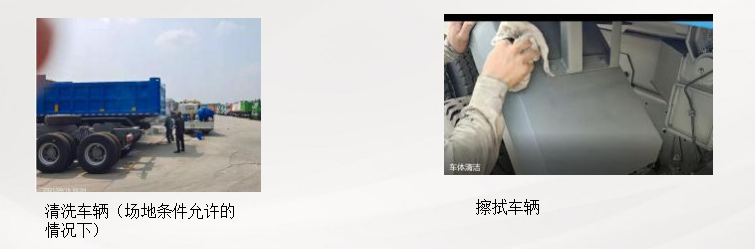
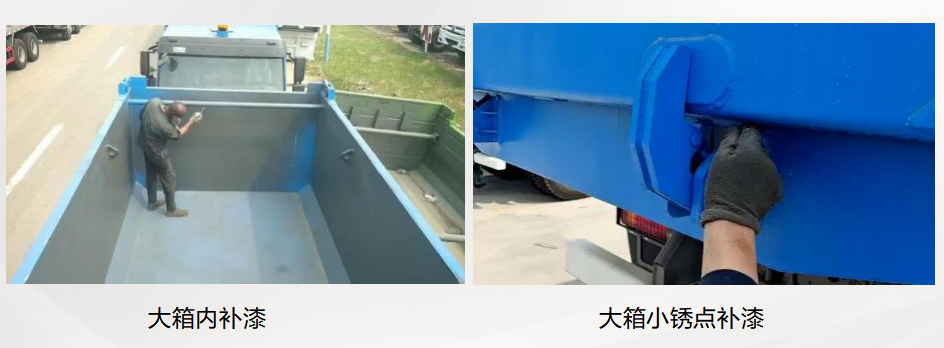
- Grease Protection
Joints of various movable parts, such as: both ends of the drive shaft, leaf springs, leaf spring seats, muffler brackets, connecting parts on the transmission; U-bolts.
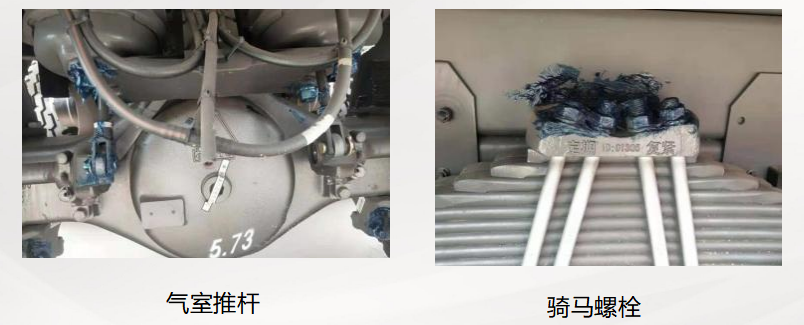
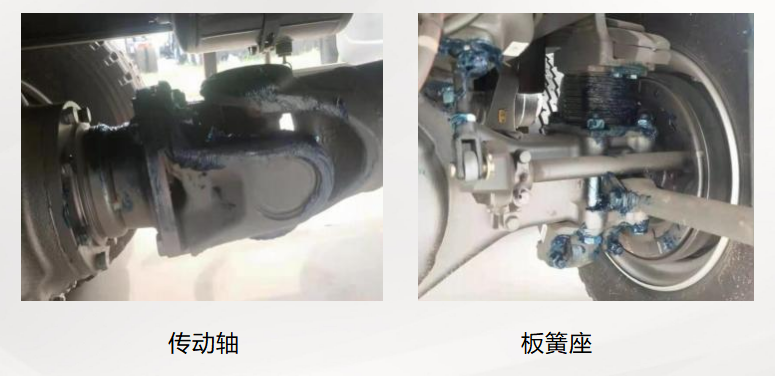
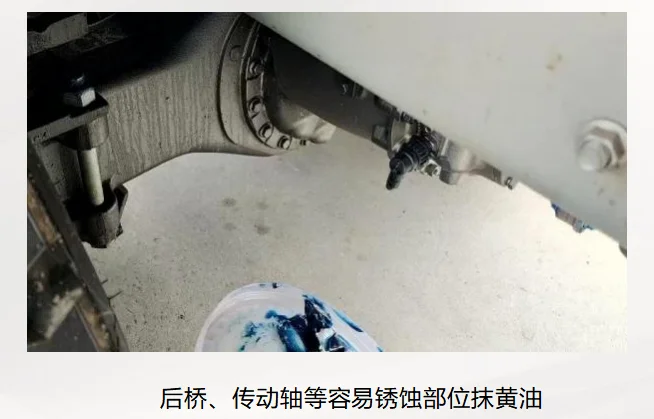
- Covering
Use newspapers, paper adhesive tapes and masking films to cover the engine cylinder head, exhaust pipes, muffler components and assemblies, and it is required to cover them tightly.
Notes:
Cover the parts that do not need wax spraying. When covering, avoid bumping the paint film to prevent secondary damage.分享
- Adjustment of Protective Wax Viscosity
Shake the protective wax well and measure the viscosity of the wax liquid with a No. 4 Ford cup. Under the working conditions of 10°C to 35°C, adjust the viscosity of the wax liquid to the specified range (when the temperature is low, take the upper limit of the viscosity value; when the temperature is high, take the lower limit of the viscosity value). If the viscosity of the wax liquid is higher than the specified value, use a special solvent for adjustment; if the viscosity of the wax liquid is lower than the specified value, open the lid of the barrel and let it volatilize naturally for a period of time before testing again until the viscosity value is within the specified range.
Notes:
The spraying environment should be clean to prevent sundries from falling and contaminating the wax film.
- Wax Spraying
(1) Use a spray gun to spray the adjusted wax liquid, and it is required to be evenly sprayed without any running or missing areas.
(2) Spraying sequence: First, spray the protective wax separately on all the exposed galvanized fasteners and flange connecting parts of the chassis. Then, start from the front of the chassis and spray the transmission and the frame in sequence. When spraying the frame, start from the left side and spray from the inside to the outside of the frame in sequence. Finally, spray the rear part of the chassis (after all the chassis protection is completed, carry out the protection for the inside and outside of the cargo box). Ensure that there are no parts that are not sprayed. Control the viscosity of the protective wax within 18-28s, and the thickness of the wax film within 100-150um.
Risk Point Control:
(1) Ensure the cleanliness and dryness of the chassis surface before wax spraying.
(2) Control the consistency of the thickness of the wax film

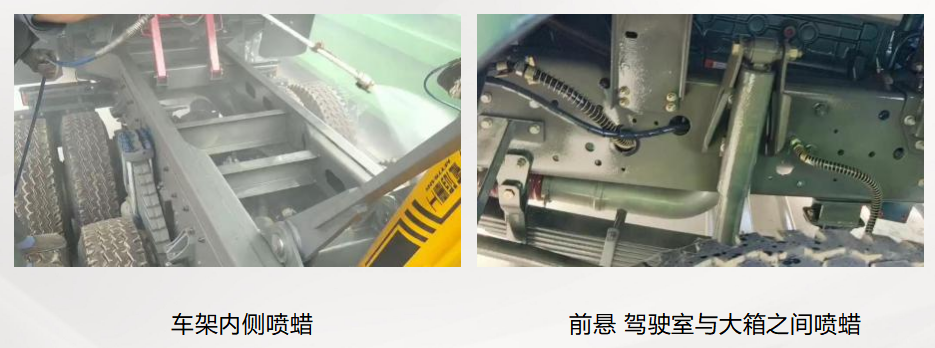
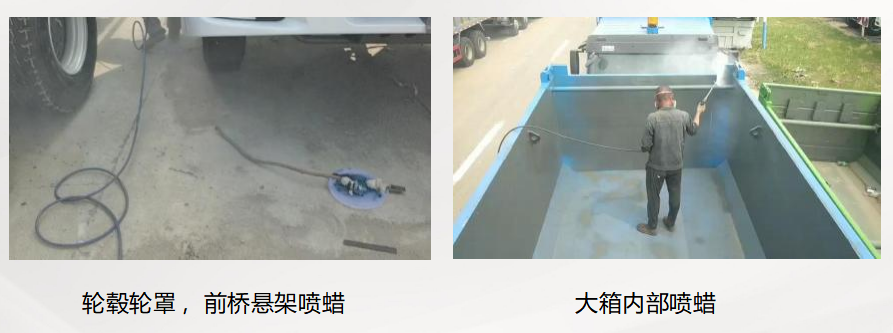
Wax spraying protection for the cargo box (including the inside and bottom of the cargo box), and be careful to avoid the rear window glass of the cab when spraying wax.
(1) Rusty parts on the superstructure of the cargo box shall be derusted and repainted according to the painting process.
Risk point: Whether the derusting of rust spots is in place.
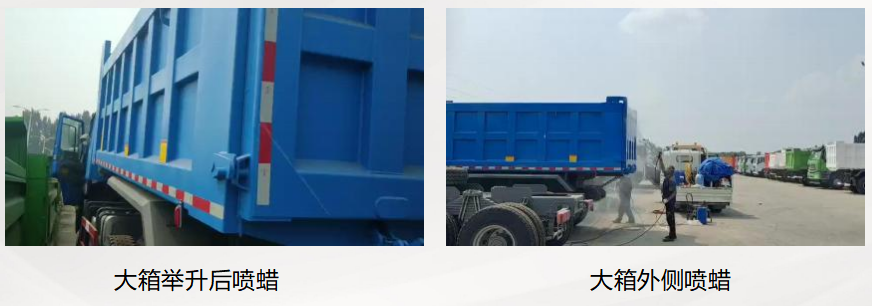
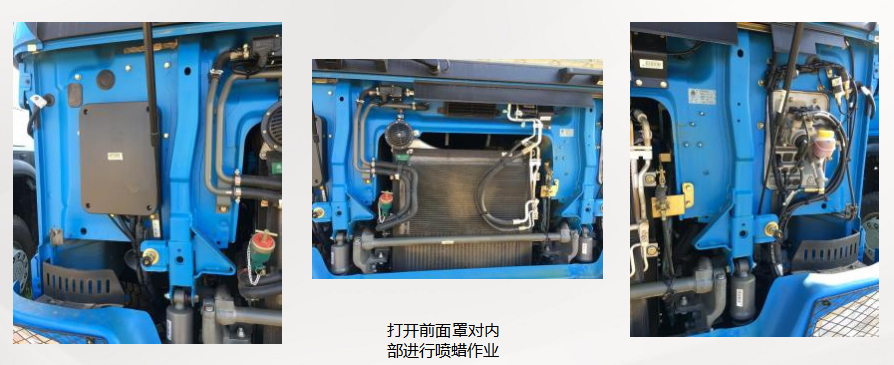
- Drying
(1) Drying conditions of the wax film:
The surface drying time of the wax film is 2 to 6 hours, and the through drying time is 24 hours (in winter); the surface drying time of the wax film is 20 to 40 minutes, and the through drying time is 24 hours (in summer).
(2) The environment should be clean to prevent sundries from falling on the surface of the wax film. - Inspection and Removal of Masking
(1) Visually inspect 100% to check whether there are any parts of the chassis that are not sprayed and whether there is any running of the wax. For the parts that are not sprayed, the protective wax needs to be supplemented, and for the appearance surfaces where the wax is running, trimming treatment is required.
(2) After the wax film is completely dry, remove the masking.
Risk point: When removing the masking, avoid damaging the wax film.
- The vehicle is transported to the destination port.
When the vehicle arrives at the port, the service station will be arranged to remove the rear – view mirrors. After removing the mirrors, the service station is required to apply grease in the bolt holes of the rear – view mirrors. - Wax spraying for leakage repair and vehicle inspection. Repaint and wax the parts with missed spraying and paint loss.
- Protect the engine starter and generator with anti – rust oil and vapor – phase anti – rust film
(1) Plastic wrap: Low – position electrical components such as starters;
(2) Apply grease: Structural components such as chassis and superstructure drive shafts. - When the vehicle is loaded onto the ship after arriving at the port, the engine and exhaust system shall be sprayed with supplementary wax. Since they are high – temperature heating components, it is impossible to spray protective wax and colorless polyurea before the vehicle is transported to the port.
- Cover with a vehicle cover.
Use a vehicle cover with reliable quality (currently, the quality of the vehicle cover is poor, like woven bags). A vehicle cover with good quality is required.
After the construction operation, after several days of exposure to the sun and a rain over the weekend, when going to observe the effect after wax spraying again on Tuesday, it is found that the effect is very good, as shown in the following picture:
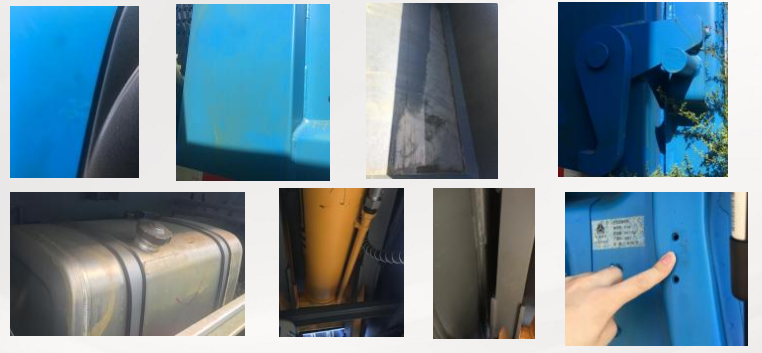
The following week, a vehicle was randomly selected for a salt spray test: Prepare concentrated brine (add table salt until it no longer dissolves), and use a spray bottle to spray the entire vehicle once. Pour 2 packs of salt into the accumulated water inside the cargo box, and then check the results after one week.
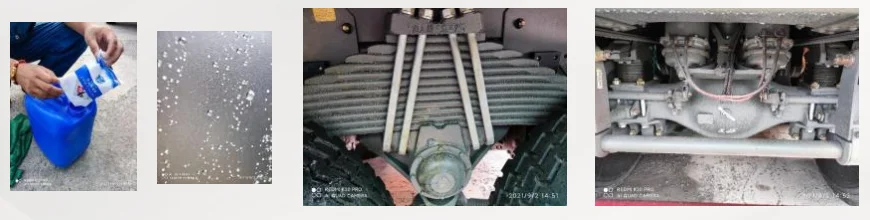
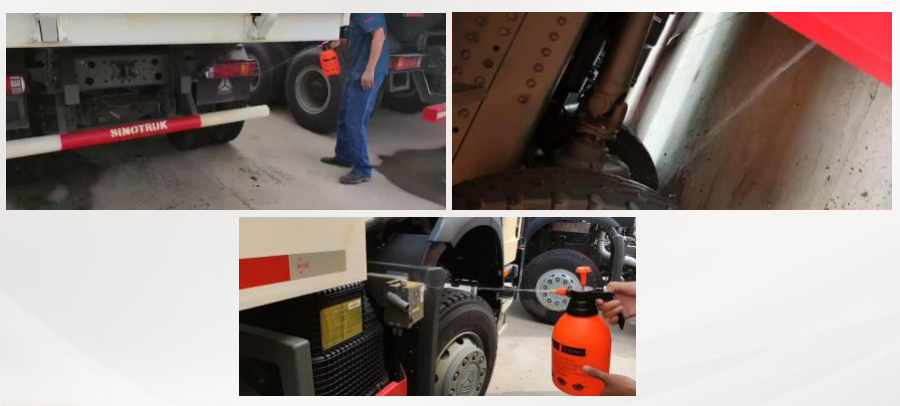
When checking again after an interval of one week, it is found that the anti – corrosion scheme of wax spraying and grease application has a very good protective effect against saltwater corrosion.
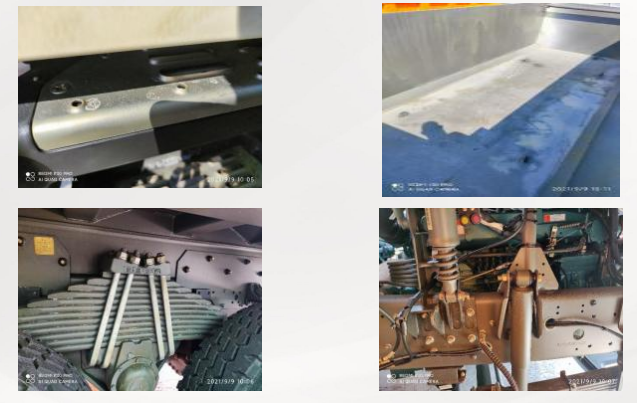